Customized Spare Parts Manufacturing
The modern manufacturing landscape demands agility, responsiveness, and the ability to produce highly customized parts efficiently. In this dynamic environment, 3D printing has emerged as transformative technologies, enabling the production of intricate and unique mechanical spare parts with unprecedented speed and precision.
Transforming Spare Parts Production:
- Addressing Obsolescence: 3D printing provides critical solutions for replacing obsolete parts. By enabling the on-demand production of replacement parts for aging equipment, these technologies extend the lifespan of valuable machinery, reducing downtime and minimizing the need for costly replacements.
- Enabling Rapid Prototyping and On-Demand Manufacturing: 3D printing facilitates rapid prototyping, allowing for quick iterations and design refinements. Moreover, 3D printing enable on-demand manufacturing, reducing lead times and minimizing inventory costs. This agility is crucial for businesses that need to respond quickly to changing market demands and unforeseen maintenance requirements.
- Driving Innovation: The combination of 3D printing empowers manufacturers to embrace innovation and explore new frontiers in spare parts design and production. These technologies enable the creation of highly customized parts with intricate geometries and tailored functionalities, addressing the unique needs of various industries, including aerospace, medical, and automotive.
Additive Manufacturing
One of the most significant advantages of 3D printing in the context of customized spare parts manufacturing lies in its ability to unlock the potential of complex geometries.
- Breaking Free from Design Limitations: Traditional manufacturing methods often impose constraints on the shapes and features that can be produced. 3D printing, however, transcends these limitations. By building parts layer-by-layer, it allows for the creation of intricate internal channels, complex curves, lightweight lattice structures, and other features that would be impossible or prohibitively expensive to achieve through conventional methods like casting or machining.
- Enabling Design Innovation: This newfound design freedom empowers engineers to explore innovative and optimized part designs. For example, they can incorporate internal cooling channels into tools, create lightweight structures with enhanced strength-to-weight ratios, or design parts with integrated features that were previously unattainable.
- Consolidating Parts: 3D printing enables the consolidation of multiple parts into a single, integrated component. This can simplify assembly, reduce part count, and improve overall system efficiency.
- Tailored Solutions for Unique Applications: In sectors like aerospace, biomedical, and automotive, where weight reduction and performance optimization are critical, 3D printing allows for the creation of highly customized parts that perfectly meet the unique demands of specific applications.
Examples:
- Aerospace: 3D printing enables the production of lightweight and complex components for aircraft, such as intricate brackets, nozzles, and internal structures.
- Biomedical: 3D printing facilitates the creation of customized implants, prosthetics, and surgical tools with intricate geometries and tailored functionalities.
- Automotive: 3D printing enables the production of lightweight and complex components for vehicles, such as engine parts, suspension components, and aerodynamic features.
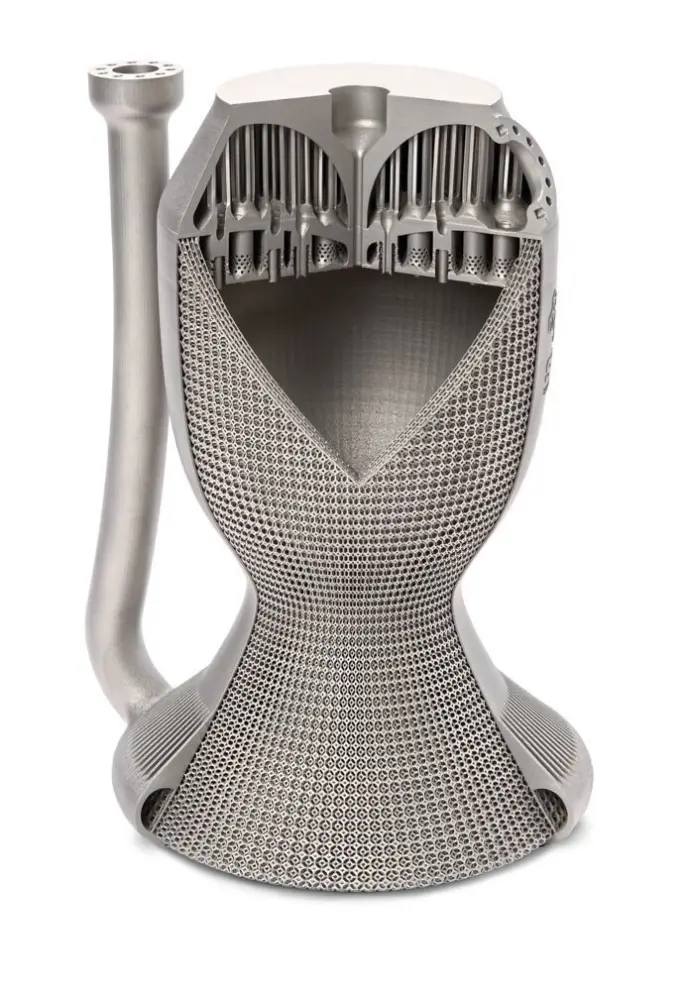